MADE IN SHEFFIELD: Medical tool company holds firm with '˜hand skills'
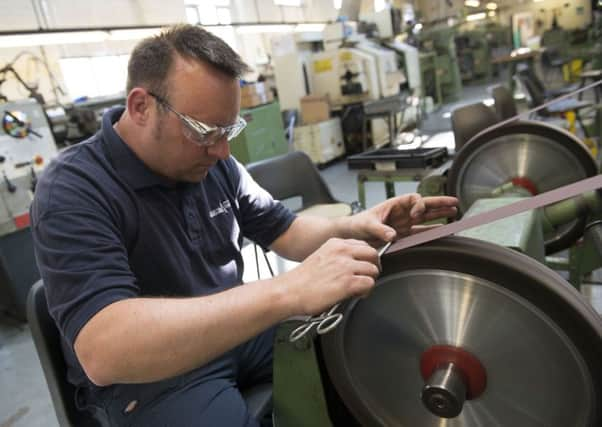

Each item can take days to put together by hand.
Skilled workers can see, feel and even hear when a component is just right, before they move on to the next step in a long, slow, labour-intensive process.
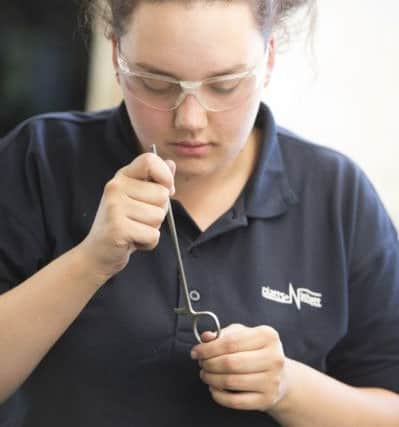

The Parkwood Springs firm is hugely out of step with manufacturing’s headlong rush into robots, automation, big data and computer power.
Advertisement
Hide AdAdvertisement
Hide AdBut bosses say surgeons love the feel, solidity and precision of their handcrafted tools. And last year was the best on record.
The firm was established by Robert Nisbett and Ken Platts in 1977. Today it is famed for a five-year, unlimited-use guarantee – and five-year apprenticeships.
But an obsession with quality never comes cheap and, with some justification, boss Alyson Nisbett says the market is awash with inferior products.
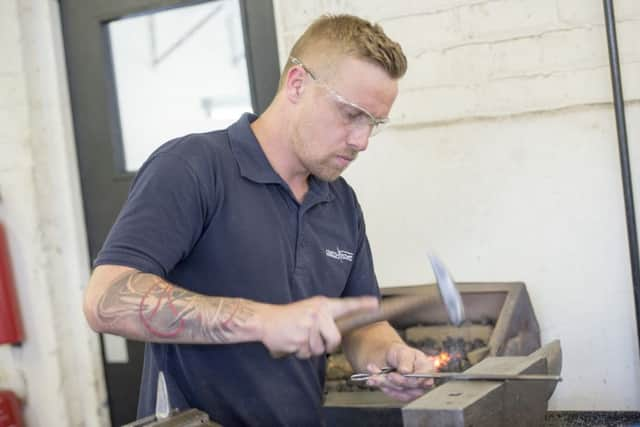

She added: “We can’t even buy the raw materials for the selling price of some of our competitors’ items, but there’s a huge gulf in quality.”
Advertisement
Hide AdAdvertisement
Hide AdJulie Topham, business development manager, added: “We encourage surgeons to come and see the instruments being made. They are shocked at the number of processes, controls and skills involved.”
Skills are most manufacturers big problem and Platts & Nisbett is no different.
Julie says they have a pile of CVs from people who can use CNC machines, but people with ‘hand skills’ are all too rare.
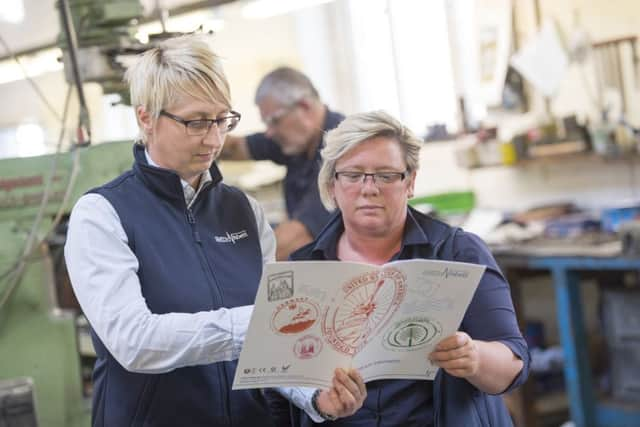

The company runs its own apprenticeship and says five years is the minimum time it takes to become an instrument fitter.
Advertisement
Hide AdAdvertisement
Hide AdAlyson: “When we put five years into a person we want them to stay. It’s hard, because a lot of firms want them.
“But we are small, friendly company which looks after people. It’s a different mindset, where people care about what they do.”
The ethos helped attract newest recruit Brooke Hawley, aged 17. The only female interviewed, she scored the highest in a practical test, Alyson said.
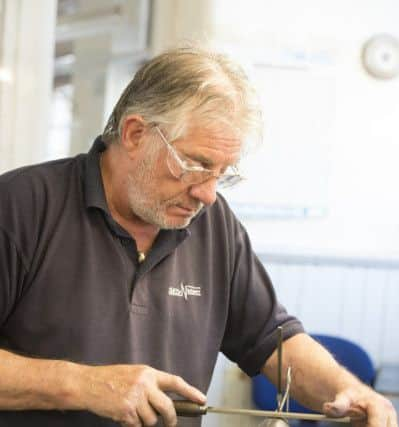

There are five women in the 22-strong firm. The first floor workshop on Woodfold, off Rutland Road, boasts multiple machine tools and workbenches. To make a self-retaining retractor involves 69 steps, starting with forged blanks, says Alyson.
Advertisement
Hide AdAdvertisement
Hide AdSkills involve drilling, hammering, filing, laser marking, milling, bending and multiple rounds of what Joe Public would call ‘polishing,’ which includes glazing, buffing and linishing. Fast spinning belts and wheels are lined up throughout the premises where Brooke Hawley is filing the bows of a forcep and foreman Mick Canetti is putting the teeth on to the jaws of a clamp.
Surgical instrument maker Carl Hinchliffe is ‘shaping to the pattern’ and fitter Paul Anderson is ‘putting through’ – joining the two parts – of a clamp by heating and hammering them together.
Platts & Nisbett makes 3,000 products and exports to 30 countries. It also sells directly to the NHS and unbranded items to ‘middlemen,’ as well as to global firms.
New transparency regulations in 2020 are expected to give the firm a boost. And while P&N can guarantee to make an identical replica of any item on its books – using the same pattern, materials and skill as the original – there is demand for new items due to the obesity crisis, says Julie. Surgeons need longer tools that can reach further.
Advertisement
Hide AdAdvertisement
Hide AdSURGICAL INSTRUMENTS MADE IN SHEFFIELD AND LOVED IN NEW ZEALAND
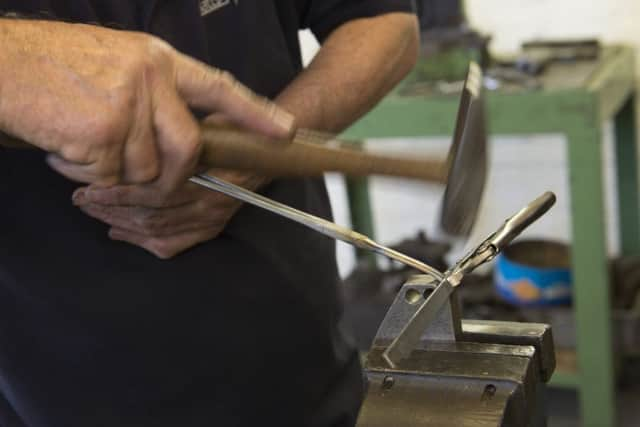

Made in Sheffield stands for quality, tradition and craftsmanship, says Alyson Nisbett, director of Platts and Nisbett.
But don’t just take her word for it.
Ann Watkin, managing director of New Zealand distributor, Downs, said: “Platts & Nisbett and ‘Made in Sheffield’ are synonymous with quality for us here in New Zealand.
“We have a long history of supplying ‘Made in Sheffield’ surgical instruments to all our hospitals. We and our hospital clients trust the quality and the fact that they are manufactured with great care, using high quality materials.”
With a recommendation like that it is little wonder export is a big target for the Sheffield firm.